Herr Hannemann, sie sind untrennbar mit Deutschlands erfolgreichstem Ultraleichtflugzeug verbunden. Wie war denn Ihr fliegerischer Werdegang?
Als Kind habe ich mich schon mit Modellbau beschäftigt. Ich erlernte das Segelfliegen 1971 auf dem Militärflugplatz Eggersdorf bei Berlin. Bei der Gesellschaft für Sport und Technik kostete der Monatsbeitrag nur 50 Pfennig. An meiner West-Verwandtschaft scheiterte eine Karriere als Jagdpilot, dafür wurde ich Wartungsingenieur im Fachgebiet Triebwerk/ Zelle und machte dazu eine Facharbeiterausbildung zum Industriemechaniker. Später war ich wissenschaftlicher Assistent am Lehrstuhl für Aerodynamik und Flugmechanik. Es war aber abzusehen, dass es im gesamtdeutschen Militär für mich keinen Platz geben würde, da das DDR-Offizierskorps viel zu groß war. Es gab dort übrigens noch einen anderen Jörg Hannemann im Range eines Majors, mit dem ich später häufiger verwechselt wurde. Da kam mir sehr gelegen, dass Comco Ikarus einen Werkstattleiter suchte. Der Kontakt kam über meine Wettkampffliegerei zustande. Da konnte ich in meinem Fachgebiet bleiben.
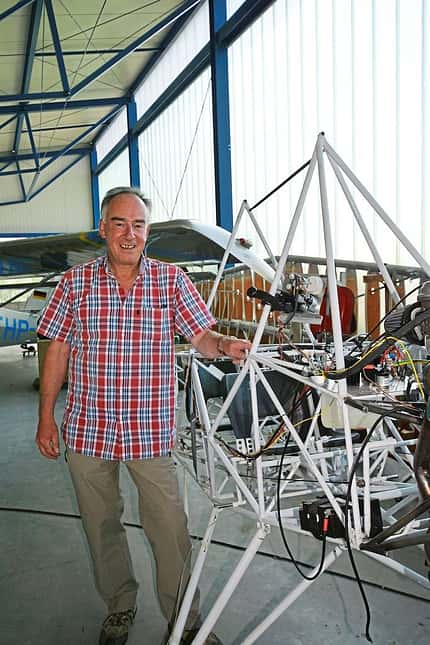
Wie sind Sie bei Comco Ikarus unentbehrlich geworden?
Mein Job sind nach wie vor die Endabnahme und die Qualitätssicherung. Ich nehme jedes Flugzeug persönlich ab. Bis heute treibt mich mein Perfektionismus an, unsere Maschinen stetig weiterzuentwickeln. Das analytische, technische Fliegen ist meine große Stärke. Dabei habe ich gar keine Testpilotenausbildung, ich habe nur mal ein paar Lehrgänge gemacht. Es mag bessere Flieger und bessere Entwickler als mich geben, aber wenige bringen beides so gut zusammen.
Wie sieht die Arbeit als Werkspilot hinsichtlich Entwicklung und Herstellung aus?
Die anfängliche Flugzeugentwicklung ist mit „trial & error“ am besten zu beschreiben, das war schon abenteuerlich. Teilweise flog man tief über die Bahn und schaute dann, was am Flugzeug noch dran war. Vom Ausprobieren kam ich dann auf die
Modifikationen unseres Rohrbausystems. Meine Aufgabe ist es, dem Flugzeug die gutmütigen Flugeigenschaften beizubringen, die wir haben wollen. Das Flugzeug soll vor allem unkompliziert sein, das ist unser Hauptaspekt. Meine Erfahrungen sind auch bei anderen Herstellern gefragt.
Sie haben 3700 Stunden auf der C42, die als Brot- und Butter-Flugzeug der UL-Szene gilt. Mit welchen Gefühlen steigen Sie heute in diesen UL-Klassiker ein?
Die C42 ist für mich gar kein Klassiker, da sie immer noch in der Weiterentwicklung ist. Aus dem Prototyp C52 ist die CS hervorgegangen, die sich viel agiler fliegt und zum Turnen verleitet. Daher macht mir die C42 immer noch Spaß. Oft das gleiche Flugzeug zu fliegen macht zudem sensibler, zum Beispiel für Geräusche.
Sind Sie bei einem Abnahmeflug schon mal wirklich ins Schwitzen gekommen, weil es Probleme gab?
Bei der Abnahme ist noch nichts Schlimmes passiert. Anders sieht es da bei der Flugerprobung aus. Ich bin schon ohne Höhenruder gelandet, nur mit der Trimmung. Das kam dem Lernprozess bei der Produktion zugute. Ans Eingemachte ging es bei der Trudel- und Flattererprobung.
Warum hatte die C42 das Zeug zum Verkaufsschlager?
Unsere Produktion ist vor allem wirtschaftlich, was sonst kaum ein Hersteller schafft. Das kommt auch beim Kunden an. Und er kauft bei uns neben dem Flugzeug das Vertriebs- und Partnernetz mit.
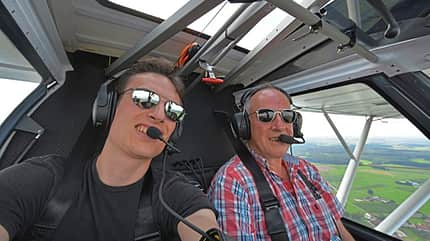
Wie sehen Sie Ihre Zukunft angesichts des Trends zu Hightech-ULs mit EFIS und Einziehfahrwerk?
Auch die Herstellung der C42 ist Hightech, beispielsweise die Qualität der Bespannung und die Herstellung des Rohrrahmens. Hinsichtlich der CFK-Flieger schlagen zwei Seelen in meiner Brust: Zum einen sehe ich die Idee des Ultraleichtfliegens auf den Kopf gestellt. Ich glaube, dass 80 Prozent der Piloten fliegerisch mit solchen Geräten überfordert sind. Zum anderen ist CFK kein so ehrliches Material wie Blech oder auch GFK, da man eine Vorschädigung kaum erkennt. Einen Weißbruch erkennt auch ein Prüfer von außen nicht, und wer lässt schon sein Flugzeug regelmäßig auseinandernehmen? Verbogenes Metall ist dagegen leicht zu erkennen. Als Ingenieur bin ich fasziniert von der Herausforderung, aerodynamisch und materialtechnisch möglichst viel aus einem Flugzeug herauszuholen. Allerdings ist nicht alles Mögliche auch sinnvoll.
Welche Perspektiven hat die Konstruktion angesichts der diskutierten Erhöhung der maximalen Abflugmasse auf 600 Kilogramm für ULs?
Was die C42 betrifft, wird die Bauweise gleich bleiben. Außerdem existiert mit der C42E schon ein Flugzeug mit einer maximalen Startmasse von 540 Kilogramm. Entscheidend ist ohnehin die Zuladung, nicht schwerere Flugzeuge. Zudem werden die Flugleistungen bei mehr Gewicht schlechter. Nicht nur die Mindestfahrt erhöht sich, bei schlechterer Steigleistung steigt auch die Lärmemission. Wir von Comco sind vorbereitet auf schwerere Flugzeuge, aber nicht im Bereich LSA. Die damit steigenden Anforderungen sind für kleine Betriebe kaum zu erfüllen.
Gibt es ein bestimmtes Flugzeug, das Sie gerne mal selber fliegen würden?
Ich baue mir derzeit eine WD3 Sunwheel, einen Doppeldecker. Seit zwei Jahren bin ich dran, nächstes Jahr wird sie hoffentlich fliegen. Die Aero L-39 Albatros interessiert mich auch, weil sie mich an meine Dienstzeit erinnert. Davon gibt es jetzt eine UL-Version, die UL-39 Albi, aber ich denke, das wird ein Experimental bleiben.
Comco Ikarus
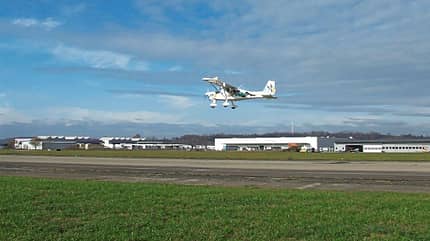
Comco Ikarus stellt seit 1970 Leichtflugzeuge her, anfangs die C22. Seit 1996 ist die C42 im Programm, die auf einer Metallrohrkonstruktion mit Bespannung aufbaut. Sie führte wiederholt die Tabelle der Jahresneuzulassungen in Deutschland an und wird auch exportiert.
Bisher wurden mehr als 1500 Maschinen in 40 Länder ausgeliefert, darunter auch beschussfeste Militärversionen und Agrarflugzeuge.
Die C42 ist auch wegen ihrer gutmütigen Flugeigenschaften ein beliebtes Schulflugzeug. Sie wird komplett in Deutschland produziert.
aerokurier Ausgabe 09/2016